The word robot means forced labor in Czech, which was for the first robot in the 1920s. The first industrial machines made an appearance in the 1960s in an automotive assembly plant. Scientifically defined, a robot is a programmable, automatically controlled manipulator, which is programmable either three axes or more.
This is a pattern well known in the history of mankind. With the new technological advancements arriving every 50 years, jobs that don’t require too much diversity become obsolete, and they are replaced with technology. Automation is a process of replacing men’s workforce and introducing a process who can do it all the actions itself, and involving only one person who has the task of overseeing it.
With the innovation, however, comes the necessity for cost estimation and efficiency within the total cost of ownership, a process SEER for Hardware from Galorath aims to solve.
So, we can see that work positions have shifted massively in the last century. Some jobs have died out, and some new ones arrived at the stage. machines can be considered to be a whole new level of automation that will provide a whole new touch to the world of work. We can see that there are some countries that are leaders in this industry. The most prominent ones are China, Japan, South Korea, the United States, and Germany.
Industrial robots in the manufacturing industry are considered robots that can perform repetitive or dangerous tasks requiring high accuracy. So, it should come as a surprise that so many companies have become interested in introducing it as the concept that will replace a high number of their workers and make the process much smoother than it was. Therefore, we would like to provide you with some of the most important industrial computer applications. Some of the applications of industrial robots include:
1. Arc Welding
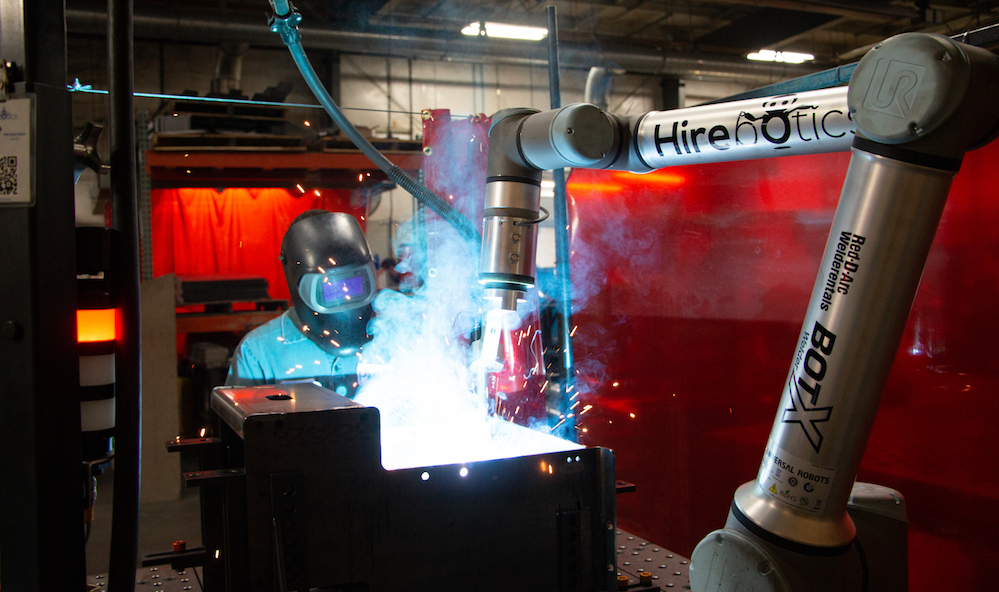
Arc welding, also known as robot welding, became popular in the 1980s. One of the top reasons for turning to arc welding was to improve the workers’ safety at the workplace from inhaling dangerous fumes and arc urns. Besides wanting to make these processes automated and having a lower number of workers in a company, another important element became the safety of the people who would work in similar positions. Surely, we are talking about one of the most important ones, without a doubt.
2. Spot Welding
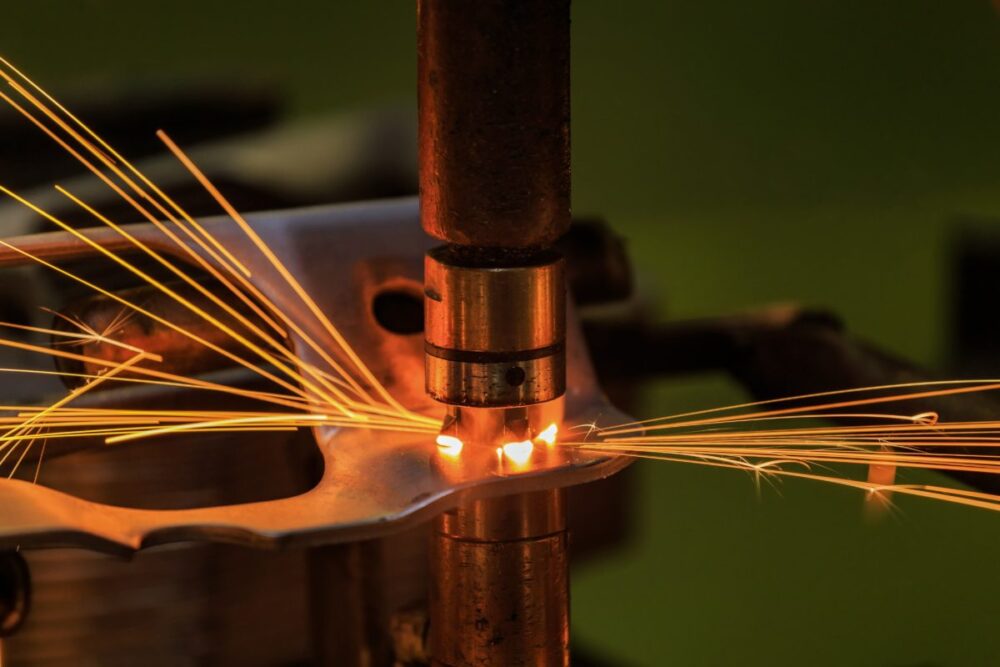
Spot welding welds two metal surfaces via a large current in the same spot, melting the metal and forms a weld in a short time, about ten milliseconds. Automatons perform this task faster and with a higher accuracy degree. Surely, we are talking about a process that requires the highest possible precision in order to have the ultimate precision.
3. Material Handling
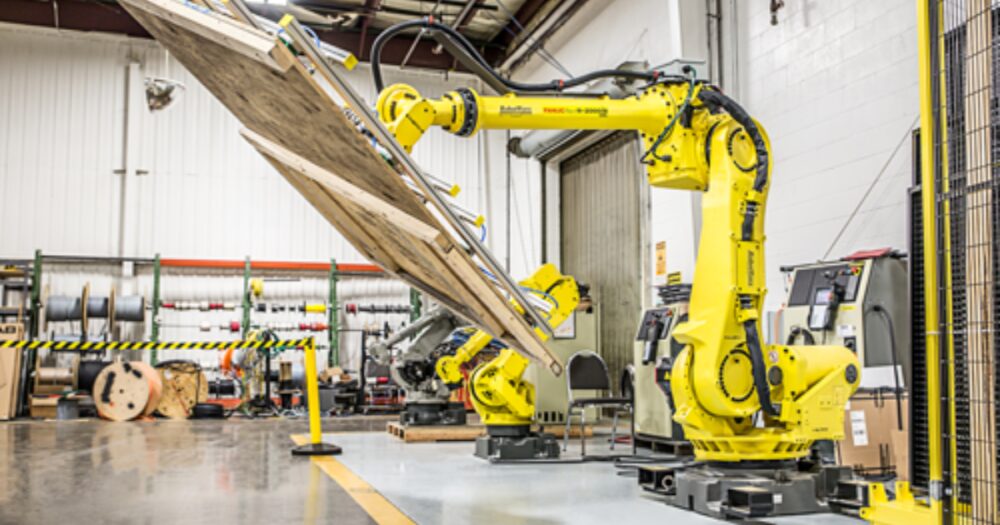
Material handling robots are used for moving, packing, and selecting products. The machines can also automate transferring and moving parts from a single piece of equipment to the other. This reduces direct labor costs and spares the human workers from performing these dangerous tasks. It should be said that some of the materials are not safe for humans to use. Therefore, it shouldn’t come as a surprise that many of these have been replaced with machines who can do this job equally well.
4. Machine Tending
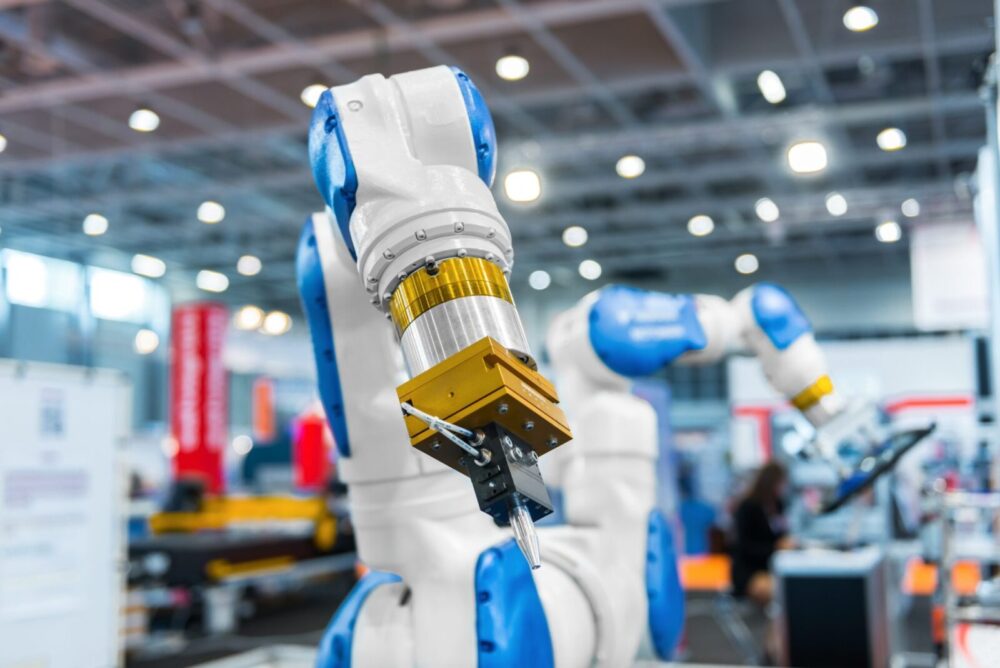
Machine tending automation is a process that involves loading and unloading of raw materials into machines for processing, and the overseeing or supervision of the machine while it works. Surely, before the introduction of the machine, people have been responsible for this task. However, it should be said that these processes can be damaging to human health. Therefore, it makes sense that they were replaced with machines.
5. Painting
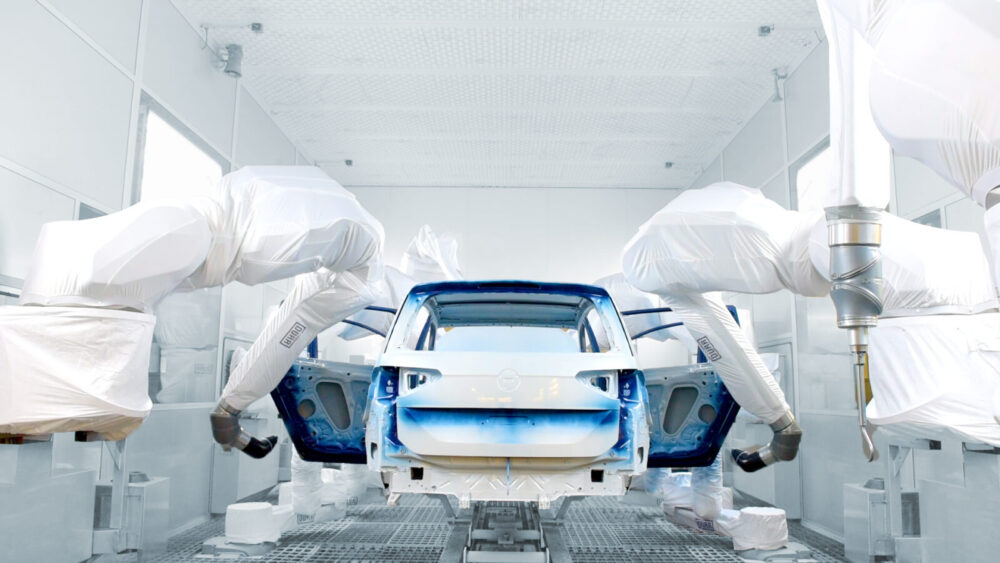
Robotic painting is familiar with the automotive assembly and other industries. Automotive painting is incredibly sensitive and requires consistency and accuracy. Mechanical painting improves the quality and consistency of the paint job and saves money by reducing waste. We are talking about a highly repetitive process that doesn’t require too much diversity, but there is a chance of having some waste. Therefore, making it automated will provide you with preventing the waste that occurs from time to time.
6. Picking, Packing, and Palletizing
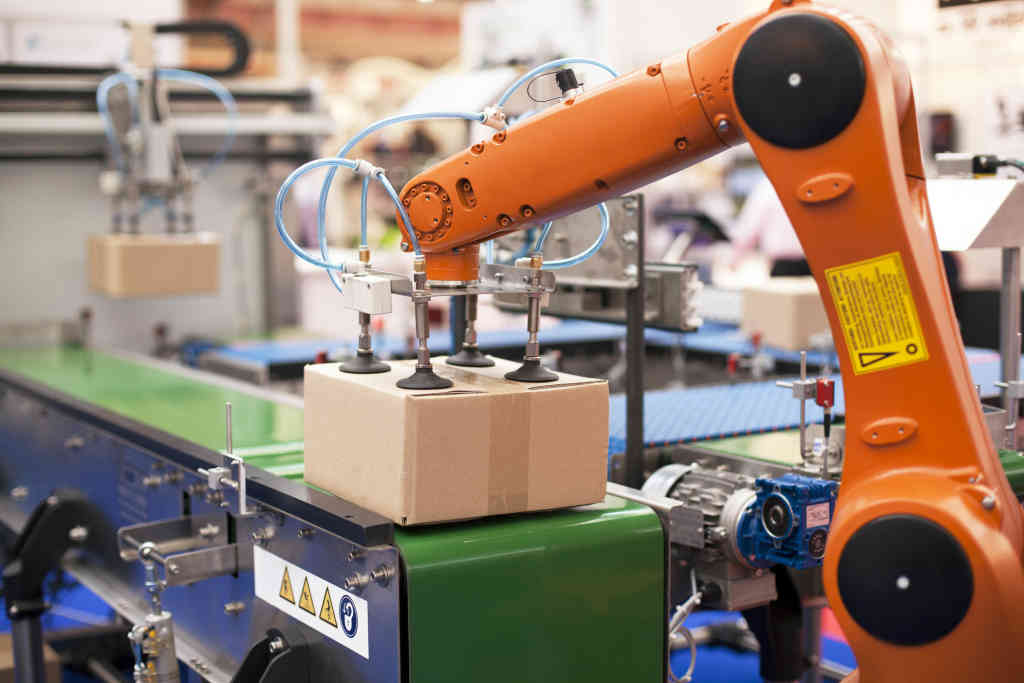
Most products go through multiple handling, from production to the final shipping. Machine packing, packing, and eventual packaging improve on accuracy, speed, and lower the costs of production. The robots’ speed improves production and efficiency from production to packaging. Once again, we are talking about a process that doesn’t require too much versatility, and it’s pretty much the same during to whole time. You can get an idea about how easier it would be to have it automatized.
7. Assembly
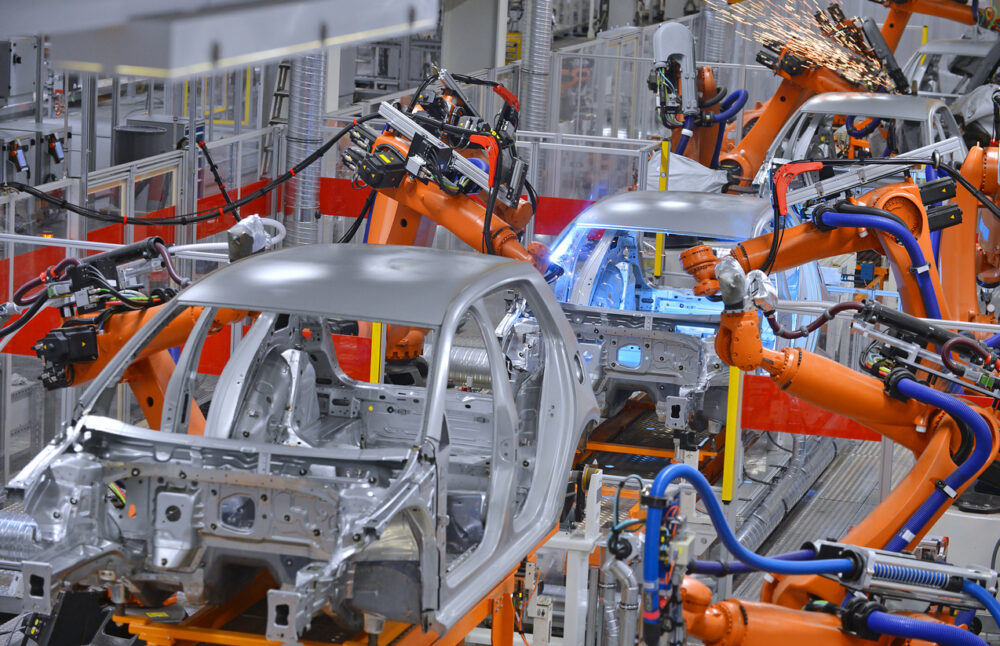
Machines are used in all assembly parts, which relieve human workers from doing tedious and dangerous tasks. Machines increase productivity and reduce costs of operations by more than half. These reasons alone should make perfect sense when talking about why every company in this line of work should invest in automating this process.
8. Mechanical Cutting, Grinding, and Polishing
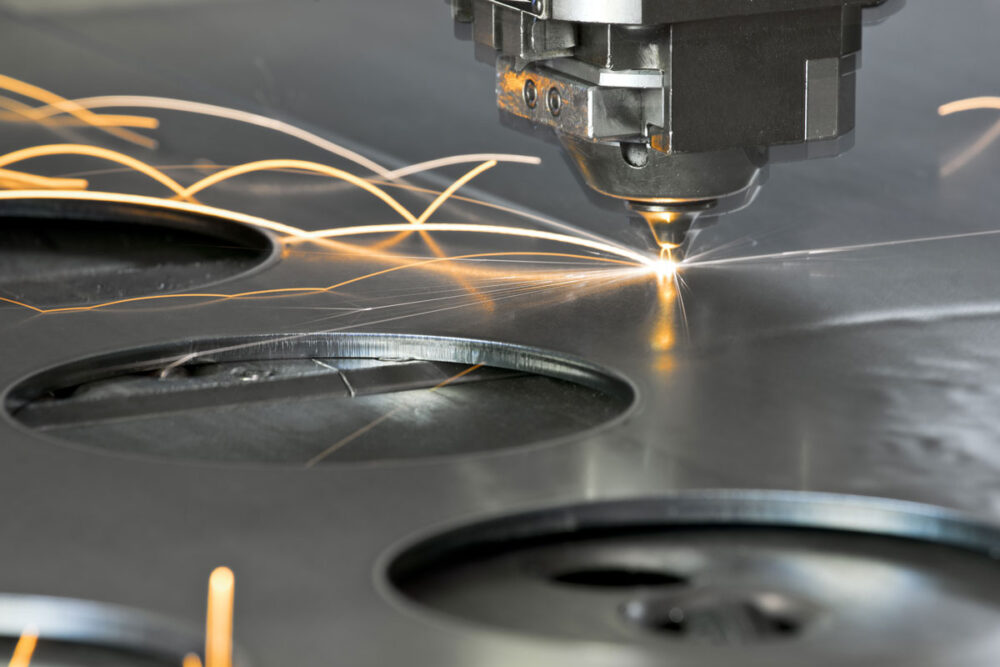
Most industrial robots are built with agility, which is an option that is hard to automate. An example is producing orthopedic implants such as hip and knee joints. Polishing and buffing a knee joint takes a human worker approximately 45 to 90 minutes. A machine can finish the same task in a few minutes using incredible speed and precision. This is the reason why these are included in the automotive industry. If you want to take a look at how it works in this industry, take a look at Universal-Robots.
9. Adhesive Sealing, Spraying Materials, and Gluing
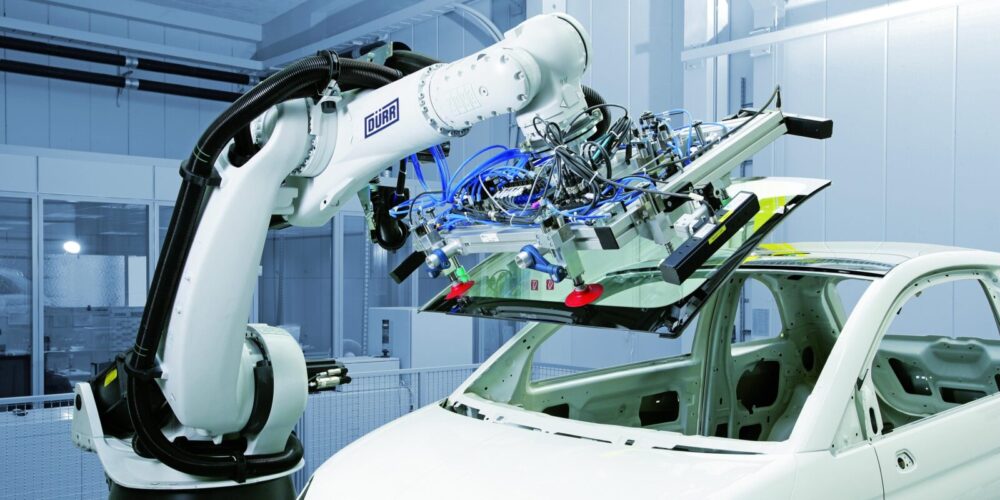
Sealer robots have many robotic arm configurations, which allow the robot to apply adhesives to all sorts of products. This application’s main advantage is the increase in consistency, speed, and quality of the products. Robots have a high accuracy level, which is needed when applying adhesives to very tiny parts. It goes without saying that machines will have a much higher precision rate than humans. So it’s no surprise that companies saw all the benefits that can arise from these processes being automatized.
10. Water jetting
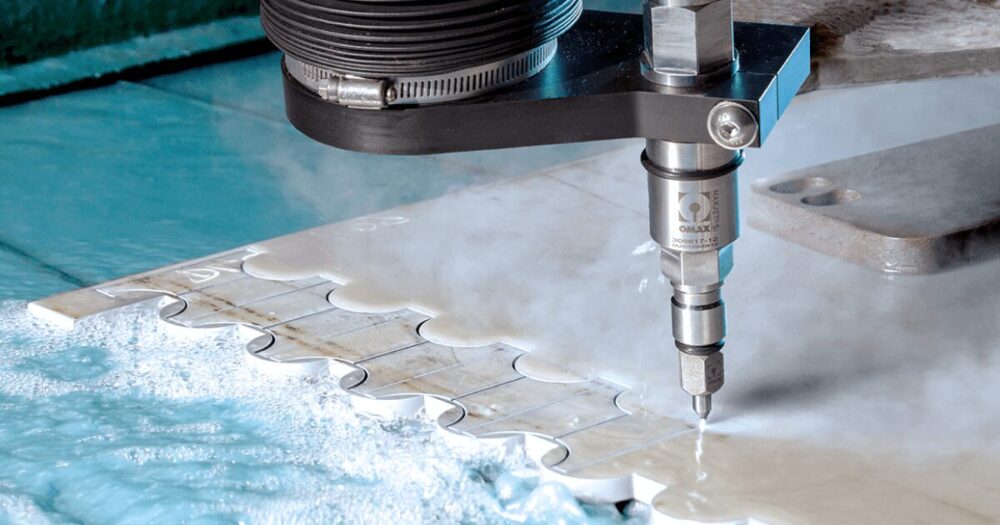
Water jets use high-pressure water combined with abrasives that help to slice titanium of not more than an inch thickness and controlled by a six-axis robot. This machine can maneuver the water jet nozzle across the desired part. A robot provides accuracy, repeatability, and rigidity, especially in fields like the aerospace industry.
Conclusion
Industrial robots have become a necessity for manufacturing plants. They make work easier and significantly increase production with their lightning speed. Where a human worker can perform a task in hours, machines can do it in minutes. The automotive industry benefits a lot from manufacturing because motor vehicles require a high accuracy degree with no space for mistakes.
Painting automobiles is another job that needs a mechanical arm to do it because of the need for consistency. The world is heading to a point where no manufacturing company will afford to operate without robots. Human workers can never compete with a machine, and it makes sense for all manufacturing plants to invest in robotics.