When it comes to metal fabrication, there are several cutting methods available, but two of the most popular options are plasma cutting and laser cutting. Both techniques offer precise and efficient metal-cutting capabilities, but which one is the best choice for your project? In this article, we’ll explore the key differences between plasma cropping and laser cutting, and help you decide which method is the right fit for your needs.
What is Plasma Cutting?
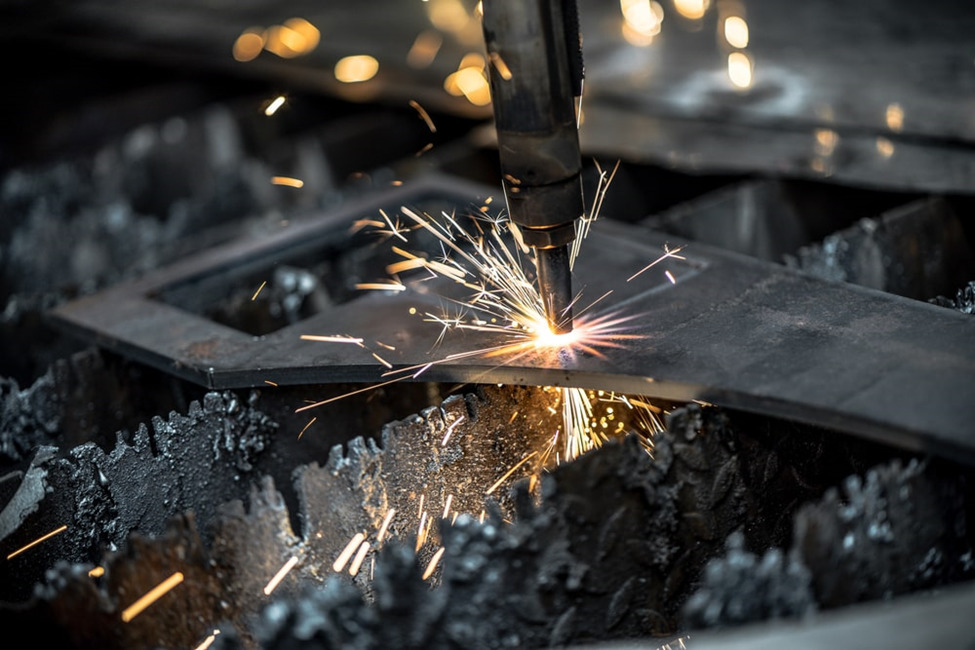
Plasma cutting is a thermal shortening process that is commonly used in CNC machine shops to cut through metal materials. The process involves creating an electrical arc between an electrode and the metal workpiece, ionizing the gas that flows through the torch to create plasma. This plasma can reach temperatures of up to 30,000 degrees Fahrenheit, allowing it to quickly and easily cut through even thick metal sheets with precision and accuracy.
Advantages of Plasma Cutting
Plasma cutting is a highly effective cropping method that offers numerous advantages over other cropping techniques. In this section, we will explore the benefits.
Cutting Speed
One of the biggest advantages is its speed. Plasma cutters can cut through thick materials quickly and efficiently, making them a popular choice for industrial and commercial applications. Compared to other etching methods, such as oxyfuel cropping or waterjet etching, plasma cropping is often the fastest and most cost-effective option.
Wider Range of Materials
Plasma pruning can cut through a wider range of materials than other cropping methods. While some techniques are limited to ferrous metals like steel and iron, plasma cropping can also cut non-ferrous materials like aluminum and copper. This makes plasma etching a versatile cropping method that can be used for a wide range of applications.
Affordability
Compared to laser etching, plasma cropping is generally more affordable. Plasma-etching equipment is typically less expensive than cropping equipment, making it a popular choice for smaller businesses or hobbyists who want to invest in their own cropping equipment.
Less Material Waste
Plasma etching is also known for producing less material waste compared to other carving methods. Because the plasma cutter creates a narrow kerf (the amount of material removed during cropping), there is less material waste during the etching process. This not only saves on material costs but also reduces cleanup time and effort after cropping.
Disadvantages of Plasma Cutting
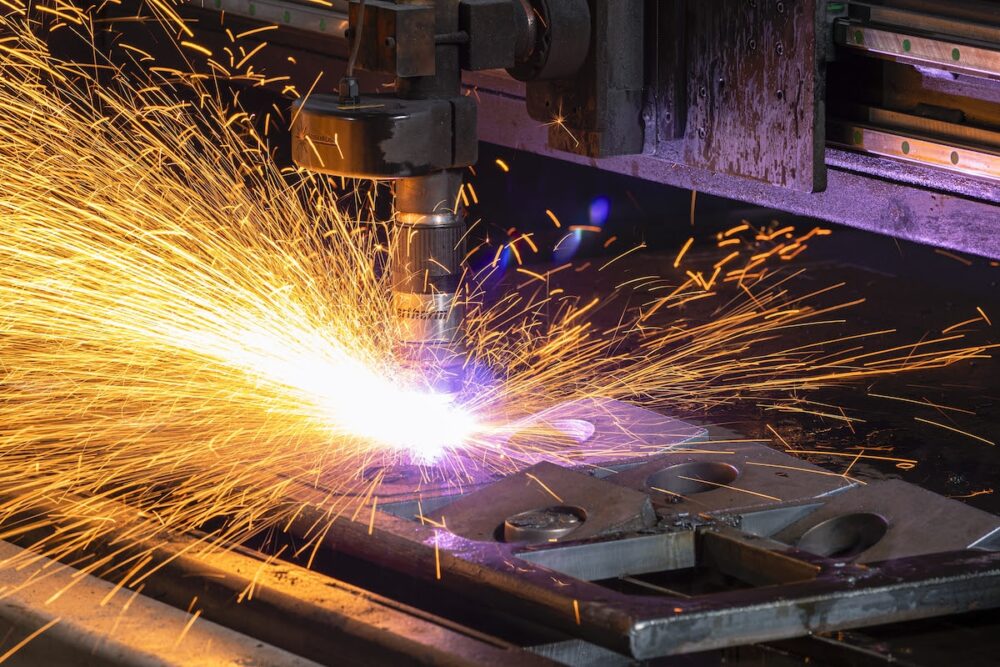
- Not as precise as laser cropping
- Can create more rough edges and dross
- May require more cleanup after cutting
- Can create more noise and fumes
What is Laser Cutting?
On the other hand, it uses a focused laser beam to melt or vaporize the material being cut. The beam is controlled by a computer program, allowing for incredibly precise cuts with minimal material waste. This etching is commonly used for trimming sheet metal, but can also be used for plastics, wood, and other materials.
Advantages of Laser Cutting
Laser cutting offers numerous advantages that make it a popular cropping method for a variety of applications. One of the primary advantages of laser slicing is its high level of precision. This pruning can produce incredibly precise cuts with clean edges, making it ideal for trimming intricate shapes or designs.
Additionally, cutting produces very little material waste, which can be important for businesses looking to reduce material costs and increase efficiency. This cropping is also versatile, able to cut a range of materials such as metal, plastic, wood, and more. With the ability to control the laser beam with computer software, laser etching can be used for both simple and complex designs. Overall, the precision, efficiency, versatility, and minimal material waste make laser carving a popular choice for a variety of industries and applications.
Disadvantages of Laser Cutting

While laser cutting offers numerous advantages, there are also some disadvantages to consider when deciding whether it is the right cropping method for your project. In this section, we will explore the potential downsides.
Cost
One of the primary disadvantages of laser cutting is its cost. Compared to other etching methods, cropping equipment can be quite expensive, which can make it a less viable option for smaller businesses or hobbyists. In addition to the initial cost of purchasing the equipment, there are also ongoing costs associated with maintaining and repairing it.
Limited Material Thickness
While laser cutting is incredibly precise, it does have limitations when it comes to the thickness of the material that can be cut. Generally, laser cropping is most effective for materials that are 0.5 inches thick or less. For thicker materials, other etching methods may be more effective.
Reflective Materials
Another disadvantage of laser trimming is that it may not be suitable for inscribing certain types of materials, particularly reflective materials. This is because the laser beam may reflect off the material instead of through it, leading to an uneven cut or damage to the laser-cropping equipment.
Safety Hazards
Laser etching also comes with safety hazards that need to be considered. The high-powered laser beam used in the cropping process can cause eye damage if proper safety precautions, such as wearing protective eyewear, are not taken. There is also the risk of fire if the laser beam comes into contact with flammable materials.
Which Cutting Method is Right for Your Project?
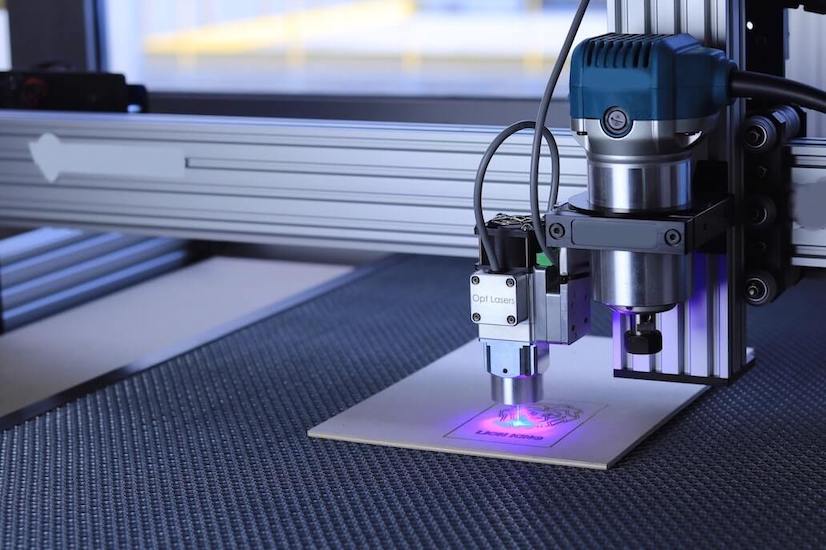
So, which prunning method is right for your project? The answer depends on a few key factors, including the materials you’re working with, the thickness of those materials, and the level of precision you require.
If you’re working with thicker materials and speed is a priority, plasma cropping may be the better choice. If you need extremely precise cuts with minimal material waste, laser etching is likely the way to go. If you’re working with non-ferrous metals like aluminum or copper, plasma trimming may be the only option.
Conclusion
Ultimately, the best way to determine which cutting method is right for your project is to consult with an experienced metal fabrication professional. They can evaluate your needs and recommend the most appropriate cutting method for your project.