Manufacturers have realised that the 2024 series is the best option if you want strong, stiff, and fatigue resistant products. The high strength alloy is always extruded to increase its functionality. That way, more impactful products can be manufactured.
These you should know!
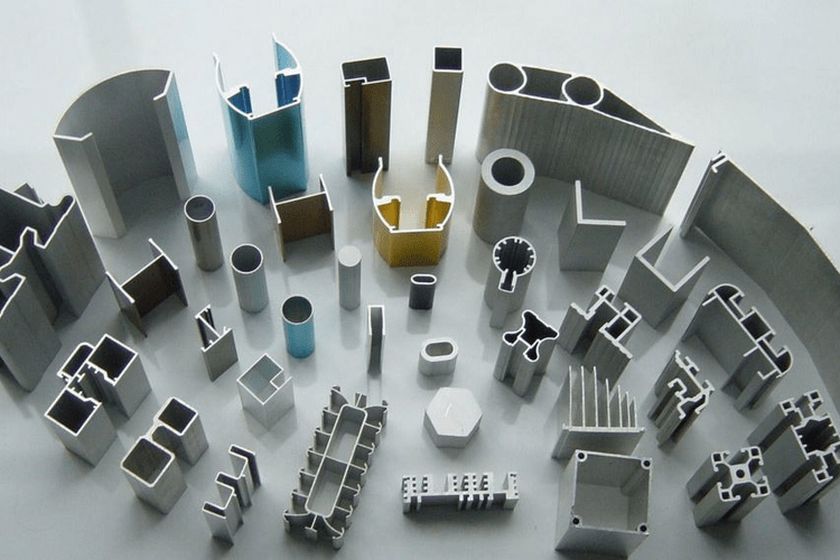
1. Ageing process
Aluminum alloys tend to harden with time. This is true especially for those alloys having little amounts of Copper, Magnesium, and Silicon. Therefore, ease or fabrication and service temperature must be considered when settling on this alloy’s Extrusion details.
2. Composition
Just like most of Aluminum Extrusion products, this alloy has its composition made of Al and other metals. Copper makes about 4.5% and has the second highest composition after the dominant Aluminum.
Magnesium and Manganese then follow distantly with 1.5 and 0.6% respectively. Then there’s Iron at 0.2% and other metals. This composition plays an important role in forming the metal’s strength qualities.
3. Mechanical properties
This alloy has an ultimate tensile strength ranging between 140 and 210 MPa. The maximum yield strength can get to is at 97. This is relatively lower than the tensile strength but defines an important aspect of the alloy. The elongation is at 10-25% stretch before the alloy fails. With these properties among others, the alloy continues to impress especially in the aerospace industry.
4. Corrosion Resistance
This alloy is said to be more prone to corrosion than others according to research. To deal with this menace, manufacturers use galvanizing process or cladding to keep the alloy long lasting. That way, the metal composition can serve better and last longer. This can be done through additional Aluminum or the manufacturer could use another alloy for the galvanization process.
5. Strengthening
Not only is this alloy strong, but can also be strengthened further using heat treatment. This is a commonly used process through which an alloy is heated to certain levels. Under such temperatures, the alloying elements get the right conditions to mix properly and form stronger alloys.
One these elements have heated enough and mixed in the right proportions, the so alloy is put in a solution through which its elements are locked up in place. It is important to note that alloy 2024 is one of the few alloys that can strengthened through this process.
The heat treatment process also determines the alloy’s optimal strength. Depending on the methods used, different tempers are formed in the process. This is the reason you have different extensions of 2024 series as far as naming is concerned, e.g. 2024-T5, 2024-T6 etc.
Applications of extruded 2024 Aluminum alloy
Due to its desirable properties, 2024 is applied in most industries today. From its strength, to high resistance to pressure, the alloy continues to impress manufacturers and thus preferred over other Aluminum metals. To boost its ability to deliver, extrusion is used! Here are some applications of 2024 extruded aluminum.
1. Aerospace
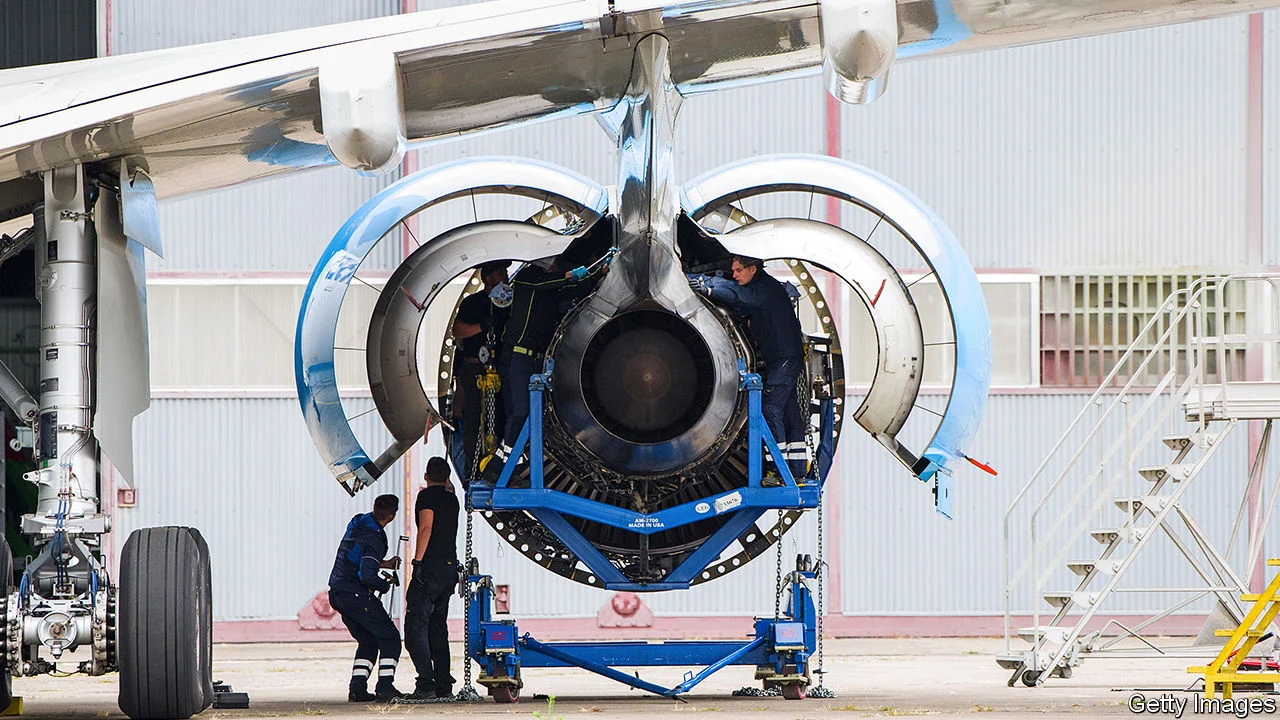
This alloy has a fair machinability rating and good workability. In addition, its excellent strength rating makes it the most suitable for aerospace designs. Just like any other alloy, this one too has weaknesses. Like earlier mentioned, the alloy has poor corrosion resistance and weldability. But these shortfalls do not affect the selection process.
Manufacturers have found ways to minimize the impact of these short comings. That way, they’re able to make this alloy even more suitable for making flying objects.
2. Building industry
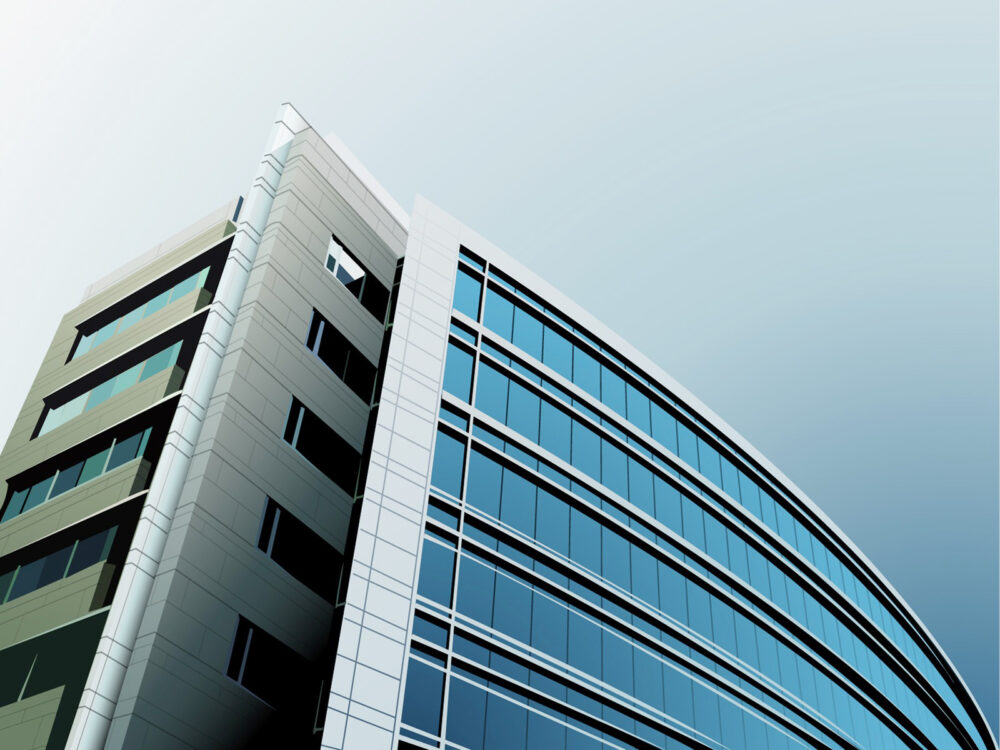
Between 2005 and 2010, there was a massive decline in the use of Aluminum in the building industry. From 2010 to now, there has been a steady rise and projections show that there will be more rise by 2024.
The 2024 Aluminum extruded alloy has been instrumental in the development of building material including doors, windows and other cladding components. There has been a rise in suburban areas developed with urban amenities. This is predicted to also rise with time. According to reports, over 300 million pounds of Aluminum would have been used by 2025.
The 2024 extruded alloy among other series make light weight building products and durable too. It is important to note that this is one of those few extrusions that make products requiring reduced maintenance. Products made of this alloy are also recycled therefore lasting longer.
You’ve also seen builders replace brick structures with Aluminum. This saves you money besides the use of long lasting metal alloys. The Extrusion process works to strengthen these Aluminum alloys as well as modify them to work even better.
3. Automotive industry
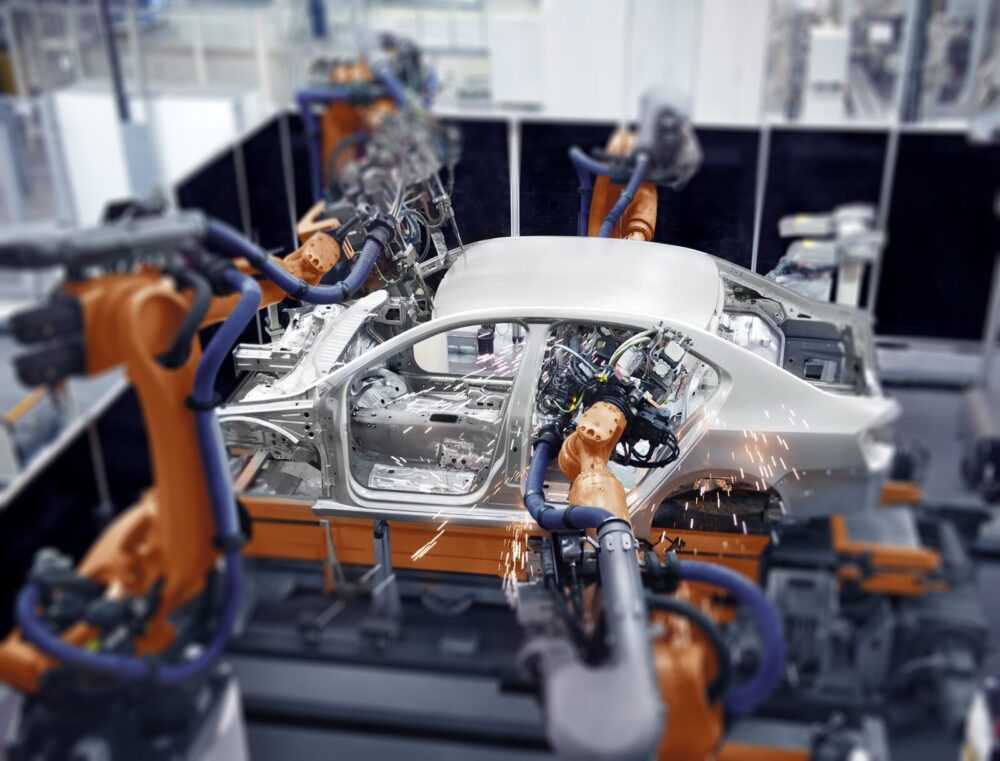
The transport industry is a big one and heavily Aluminum reliant. The 2024 extruded series is one of those Aluminum alloys that are preferred when making automotive.
Since 1800’s, the alloy has been used to develop the body of cars. It’s important to note that one car has about 30,000 parts. All these are designed to help the car perform It’s functions well. Therefore, they must be made of either similar materials or those that can be fixed together towards a similar goal.
Break components, rotors, cylinders, wheels and gears are some of the car parts made of the 2024 Aluminum alloy. Another reason why this extrusion product is preferred is its ease to form being better than that of steel.
The car bodies have an important role. Not only do they determine how the car looks like, they also protect the interior and have a direct impact on the vehicle’s functionality. Therefore, they must be designed and built in a special way using a durable material. The 2024 Aluminum extrusion alloy meets all these standards and this explains why it’s the alloy of choice for most manufacturers.
4. Electrical industry
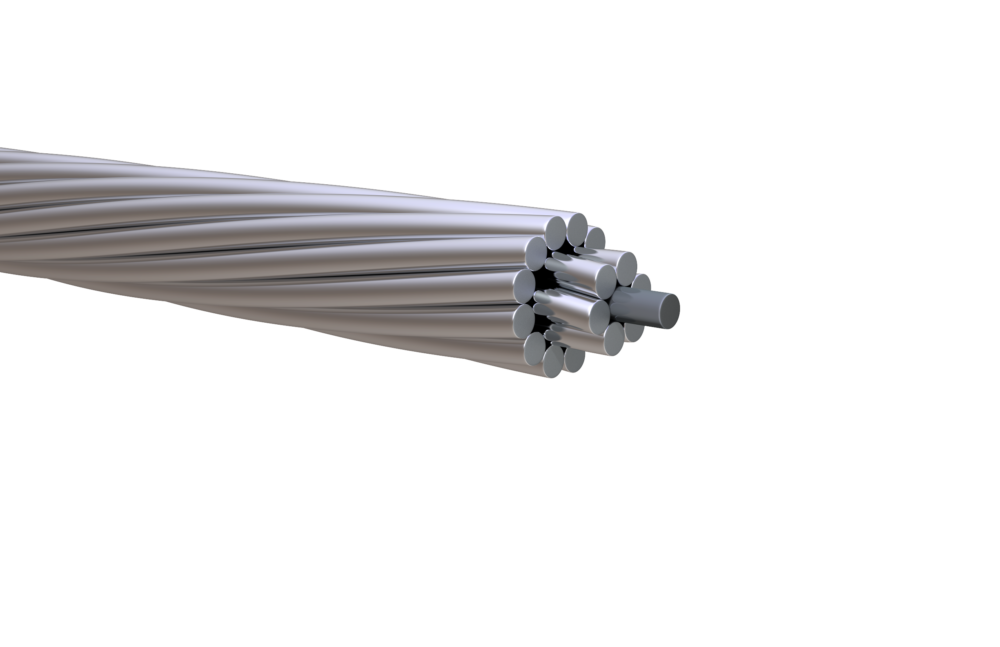
Aluminum is an excellent conductor of electricity and also durable. The alloy 2024 and others have been used to make important components of electrical systems. The extruded alloy is durable and that’s why it’s preferred over copper and other Aluminum alloys. The series may not have the best corrosion resistant properties but is sure impressive at how it works.
According to history, the first time Aluminum was used, the move was to replace a highly corrosive copper metal. Initially, copper was used to make electrical systems in the railway industry. But turns out the copper was greatly corroded with the smoke. After Aluminum’s introduction, much has changed. Time and again, drawing has been used to improve the alloy’s functionality.
Steel is also used time and again to strengthen electrical cables. This is because Aluminum’s ease of formation leaves it vulnerable to bends even when not required. Strengthening takes care of this and improves the alloy’s performance.
In the US, the National Electric Code recommends use of Aluminum in the development of new buildings. This has greatly increased the use of Aluminum. In China, similar policies were implemented in 2015. In the process, alloying and extrusion processes have greatly increased to facilitate production of ready to function alloys like the 2024 series.
Aluminum is also cheaper than copper therefore it’s preferred. Not only that, Aluminum extruded cables transmit double power or even more compared to similar copper cables. The double capacity is important especially in areas of compact planning. These areas like the congested cities with little or no space to add more power infrastructure but a growing need to increase power transmission.
The 2024 Aluminum extruded alloy is also used in radar construction, development of TV antennae and also transformers developed for low voltage transmission.
5. Consumer goods
The 2024 series is one of the most common alloys used in the manufacturing of consumer goods. Aluminum in general is preferred in development of tablet PCs, flat screen TVs, sport equipment, furniture, coffee makers, and mirrors among other products. The alloy is lighter than steel but stronger than plastic. These two would and are the alternatives. But as manufacturers realize a rise in the consumption of Aluminum products, they continue to use the alloy more as it has a direct impact on their sales.
The alloy is also preferred for its beauty and practicality. The 2024 alloy and other Aluminum extruded alloys boasts of sophistication and reliability but at the same time remains very light and robust. These are some of the features consumers go for when settling for a consumer product. In the end Aluminum extruded alloys wins.
Matte products also sell greatly. Developers have realized that alloying and anodizing Aluminum makes it a better performer. Therefore, they continue to extrude alloys like the 2024 series to make them better placed for making nice and more durable consumer products.
6. Machinery and equipment
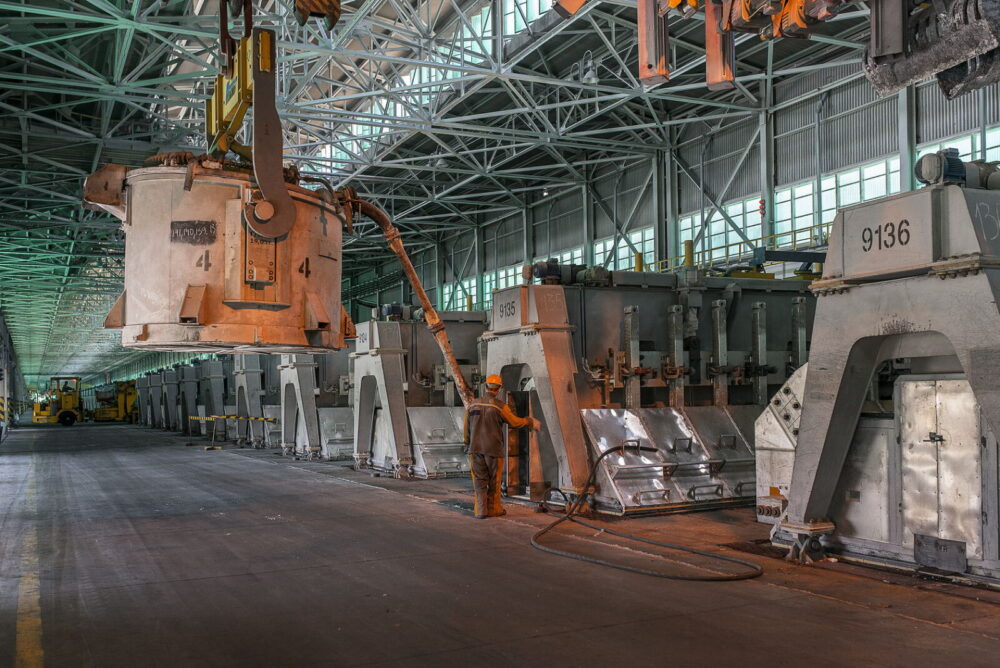
The 2024 Aluminum extrusions are also used to make machinery and equipment. Such large products require materials that will last long and also resist corrosion. This alloy boasts of such qualities among other desirable ones. Therefore, this is a proffered alloy in the machinery development process.
Conclusion
Aluminum Extrusion continues to gain popularity because of the positive impact it has in the manufacturing industry. The 2024 Aluminum series is one of the alloys which if extruded, offers greater and superior functionality.