Companies must go through a series of cost-cutting methods to ensure they land on the perfect strategy for mass production. If you can save pennies on one piece, you are saving thousands of dollars on mass production. So in the mass production of hardware products, various things must be kept in mind, including the material and design of the final product. The etching process makes things easier as users can etch the noncritical part from the layer and achieve the desired format.
So in this article, we will discuss types of etching processes as each material takes time to etch depending on the process and its internal properties.
What Is Metal Etching?
Metal etching is the process in which various substances are utilized to remove unwanted parts from the overall surface to reach the desired shape. You can easily attain different complex conditions, requiring heavy machinery and precision for mass production. This process occurs by controlling the temperature and concentration of the chemical mixture, which etches away extra metal present in the layer.
This chemical solution is prepared so that it does not react with the surface of the metal and alter its properties. This process is highly efficient as you are ready with the most delicate piece of product with the least possible faulty pieces.
Chemical Etching
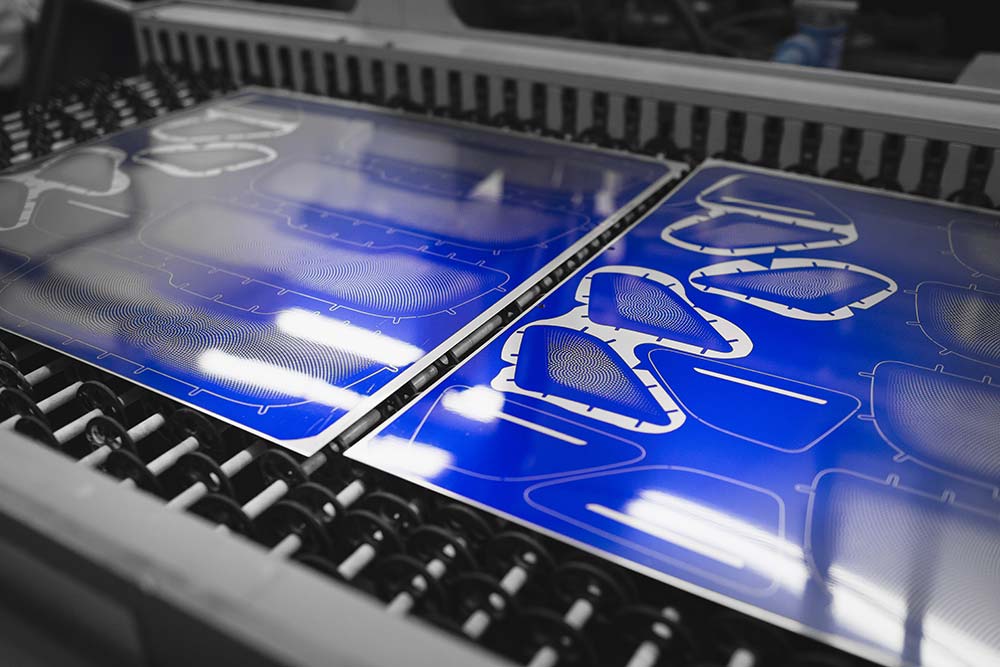
Chemical Etching metal process involves using acids, lasers, photoresistor screens, and much more, making it easier for them to attain the final product of the desired shape. This process is also known as acid etching as it works on a similar principle and removes the unwanted parts with higher concentration acids. The acid bath is prepared so that the required design is covered with a coating that prevents it from reacting with the acid. The most suitable material for such processes are metals and alloys; this process is slower in stainless steel as it is an alloy with carbon and highly refractive features.
Chemical etching is a process that occurs in a series of steps which are discussed below.
- In the primary step, the surface is cleared to ensure no dirt or debris is left on the cover.
- On the surface is cleared, a resistant layer is applied to the metal, preventing the selective part from corroding while in contact with acid. This resistant layer is mainly made up of inert elements that do not have free electrons, preventing it from reacting with parts.
- Once the resistive layer is applied, the final image of the product is imprinted on the layer to ensure that the product is etched with extreme precision.
- Now an acid bath is prepared, the acid is decided based on the reactivity series and the material, and the product is dipped in the acid bath and left for some time to etch carefully. The resistive layer prevents the final shape from being affected during the acid bath.
- When this completes the acid bath, the final product will be visible and remove the resistive layer from the surface.
- A few finishing steps need to take place, including polishing the surface and placing the final checks for mass-scale production.
Photochemical Etching
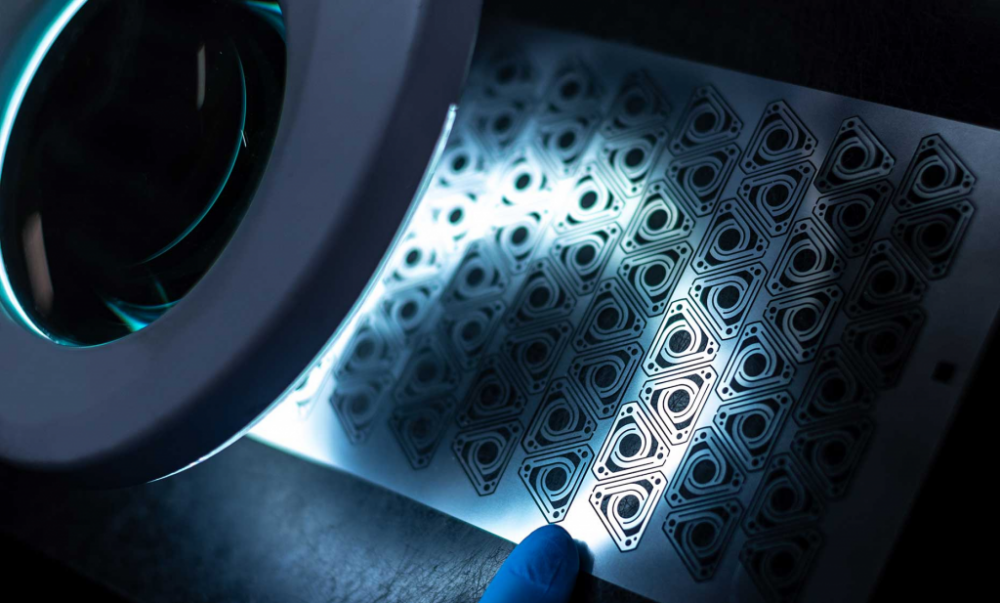
The photo term in chemistry points to using lights to complete a particular reaction. Various photosensitive materials react in the presence of light, and most of these compounds are made of silver. So let us understand the procedure of photochemical etching and how it makes it easier to develop products per the requirements.
In this procedure, CAD (Computer Aided Designs) are prepared, which make it easier for the users to determine the calculation ranging from the thickness of the layer, type of material, tolerance, and other physical properties of the metal. The procedure of photochemical etching is discussed below in detail.
- The first step of the process requires cleaning the metal to ensure that no external component like dirt can complete the process. The impurities on the material can affect the calculations as they have their resistive values and would affect the final product.
- Once the cleaning has been done, the lamination of the layer begins, and a thin photoresist layer is placed on both sides of the layer to prevent UV exposure.
- After this process, a CAD structure photoresist sheet is placed on the thin laminated sheet, exposing the product to UV rays. The outer photoresist sheet becomes hard, and the inner laminated sheet remains soft.
- Now ferric chloride is poured on the product to dissolve the thin film region leaving the laminated part unaffected.
- Once done with this process, the hard coating is removed, and the final product is obtained. The finishing checks of the material take place to ensure that the final product has flaws.
Laser Etching
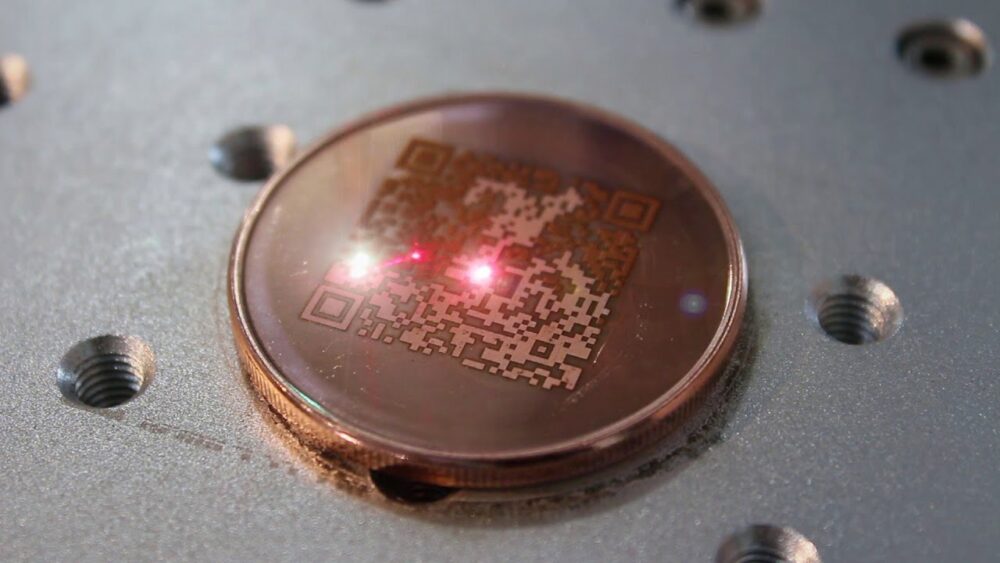
Lasers are charged rays of light directed towards the particular metal part to increase its temperature and melt it to attain the required shape. The process of laser etching has a series of processes and requires a lot of energy, but this process is quick and efficient. The working process of this method is pretty simple as the layer is directed on the hard layer, and the cuts are made to obtain the final product.
Laser etching is of two types; the first one is a flatbed etching, whereas the second one is also laser etching. The flatbed etching focuses on passing the metal sheet through a machine to cut an exact design on the sheet, whereas the galvo laser uses a mirror to reflect the laser through the surface to obtain the desired format. Various variables in this process determine the final cost, including the type of laser (Solid, Liquid, Gas, Semiconductor, and metal vapors) and the temperature resistance of the material.
Conclusion
Etching is a reliable process as it makes achieving desired results easier, but it requires extreme precision and knowledge of materials. The time metal takes to etch completely depends on atmospheric conditions along with the concentration of the acid or power of the laser. So if the time has to be minimized, there would be a hike in cost.