In the world of surface preparation and finishing, abrasivi per sabbiatura, or abrasives for sandblasting, play a crucial role. Whether you’re cleaning metal surfaces, removing rust and paint, or preparing a structure for coating, the quality and type of abrasive used can make a significant difference in efficiency, cost, and end results.
What is Sandblasting?
Sandblasting, also known as abrasive blasting, is a process that propels fine particles at high speed to clean or modify a surface. It is widely used in industries such as construction, automotive, shipbuilding, and metal fabrication.
The abrasive material used in the process is critical to its effectiveness, as different materials have different levels of hardness, density, and recyclability.
Types of Abrasives for Sandblasting
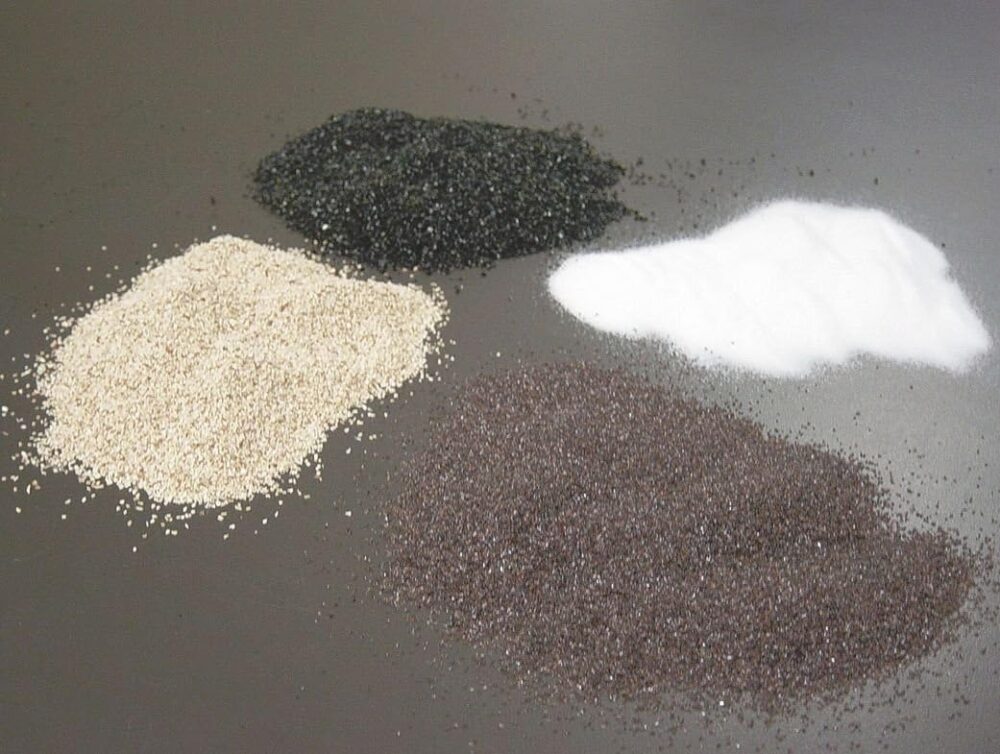
- Garnet
Garnet is a natural mineral abrasive that is sharp, hard, and reusable. It’s known for producing minimal dust, making it an environmentally friendly option for surface preparation and waterjet cutting. - Aluminum Oxide
One of the most aggressive abrasives, aluminum oxide is ideal for tough jobs such as removing paint, corrosion, and scale from metal. It is durable and reusable, often used in high-performance applications. - Steel Grit and Steel Shot
These are commonly used in industrial cleaning and surface profiling. Steel grit offers a sharp profile ideal for coatings, while steel shot is used for smoother finishes or peening applications. Both are highly recyclable. - Glass Beads
Made from lead-free, soda-lime glass, glass beads are a good choice for cleaning without damaging the underlying material. They are used for surface finishing and creating a uniform, satin-like finish on metals. - Silica Sand (Quartz Sand)
Although traditionally popular, silica sand has fallen out of favor due to health risks related to silica dust inhalation. It is now largely replaced by safer alternatives. - Crushed Glass
This recycled product is sharp and effective for removing coatings and corrosion. It is less aggressive than some other abrasives, making it suitable for more delicate surfaces. - Walnut Shells and Corn Cob
These biodegradable abrasives are used for softer cleaning applications, such as stripping paint from wood or cleaning engine components without damaging them.
How to Choose the Right Abrasive
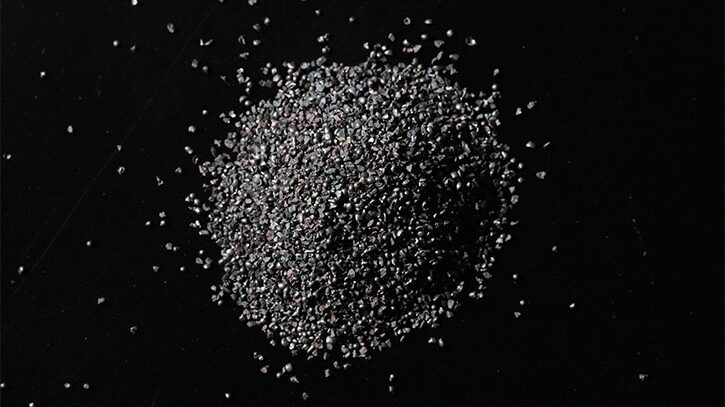
When selecting an abrasive for sandblasting, consider the following factors:
- Surface material: Softer metals or delicate surfaces require gentler abrasives like glass beads or walnut shells.
- Desired finish: Some abrasives produce a smoother finish, while others are more aggressive.
- Recyclability: For large projects or repeated use, investing in recyclable abrasives like steel grit can lower long-term costs.
- Health and safety: Always choose abrasives that meet current safety standards and minimize health risks.
Safety Considerations
Regardless of the abrasive chosen, sandblasting should always be performed using proper safety equipment, including respirators, gloves, and protective suits. Adequate ventilation and dust collection systems are also essential to maintain a safe working environment.
Conclusion
Abrasivi per sabbiatura are essential tools in many industrial processes. By understanding the properties of different abrasive materials and matching them to your specific application, you can achieve better results, reduce waste, and enhance worker safety.
As technology and environmental regulations evolve, the demand for more efficient and sustainable abrasive solutions continues to grow.
Whether you’re restoring a piece of machinery or preparing steel for a new protective coating, the right abrasive is the key to success.